An increasing number of shipowners and shipyards are investigating the potential of synthetic methane or methanol to reduce greenhouse gas (GHG) emissions.
Mitsui OSK Lines (MOL) is the latest maritime company to turn its attention to fuels that can be produced by methanation. The Japanese shipowner aims to develop synthetic methane for use on ships and establish a supply chain. Earlier this month it launched a working group dedicated to the task and joined the national Carbon Capture & Reuse (CCR) Study Group.
Synthetic methane can be produced by combining carbon dioxide and hydrogen in a process known as methanation. If the CO2 is sourced by carbon capture and the hydrogen created from renewable energy (such as wind or solar), the resulting fuel is carbon neutral. Methane is a familiar fuel in shipping as the main component of LNG. A synthetic version, using similar supply infrastructure and engines to LNG, would offer the same benefits to sulphur and nitrogen emissions while overcoming the debate around LNG’s impact on greenhouse gas emissions.
Improvements are needed both to carbon capture technologies and the process of creating renewable hydrogen in order to make synthetic methane a viable ship fuel. MOL will draw on the experience of the CCR Study Group, a consortium of Japanese industrial groups and academic institutions that has developed a road map for methanation technology development to 2050.
Practical challenges
Separately from the CCR Study Group, Mitsubishi Heavy Industries (MHI) has also been investigating the use of methanation fuel. Its CC-Meth project gives an indication of the scope of work needed to prepare the various technologies involved for use on ships. According to MHI ship and ocean engineering deputy manager Kazuki Saiki, the carbon capture and methanation equipment needed to create the fuel for a very large crude carrier would weigh around 4,500 tonnes- equivalent to around 2% of the vessel’s deadweight.
The challenges do not stop there. Using current technologies, the system would add more than US$45 million to the cost of a VLCC newbuild. Payback within the lifetime of the vessel would demand both an onerous carbon tax and an unrealistically cheap price for renewable electricity (to generate hydrogen).
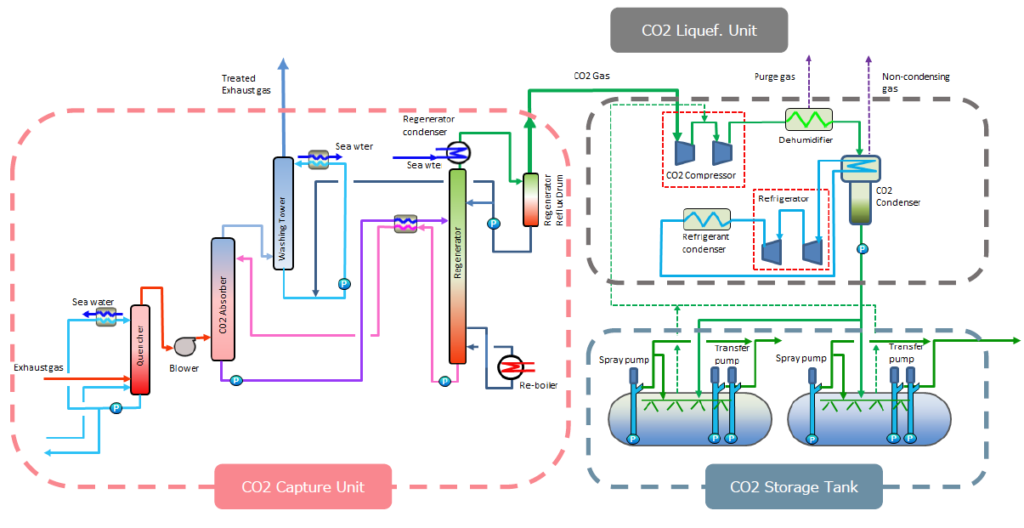
Research into the application of methanation is not confined to Japan. In Europe, the HyMethShip consortium – led by the Large Engine Competence Center (LEC) and including shipyard Meyer Werft and shipowner Exmar – is considering a ship application that would result in vessels bunkering methanation fuels but eventually burning hydrogen in their engines.
LEC area manager Jan Zelenka explains that rather than capture CO2 after methanol combustion, it is more efficient to bunker methanol and remove carbon during a process that reforms methanol to hydrogen. The captured CO2 is stored and fed back into the onshore creation of the synthetic methanol, while the resulting hydrogen is burned in the ship’s engines.
The use of waste heat from engines to reform hydrogen further improves the efficiency of the HyMethShip configuration. The consortium projects a 97% cut in GHG emissions compared to burning heavy fuel oil. Over the next three years the group will develop the new solution, including an engine (with development input from gas engine specialist INNIO Jenbacher) that will be able to run on hydrogen, methanol or diesel. The concept will be validated in an onshore demonstrator with a power output of 2MW.
The HyMethShip conveniently avoids burning methane in engines and therefore does not have to deal with the environmental challenge of methane slip. It also draws on the increasing interest that several European countries are taking in methanation fuels as ways to decarbonise their transport infrastructure. Projects such as the German E2Fuels initiative – in which MAN Energy Solutions is participating alongside Siemens, Volkswagen Group, Bösch and others – are striving to make widespread availability of synthetic fuels a reality. If synthetic methane or methanol is available onshore, it does not need to be produced on board.
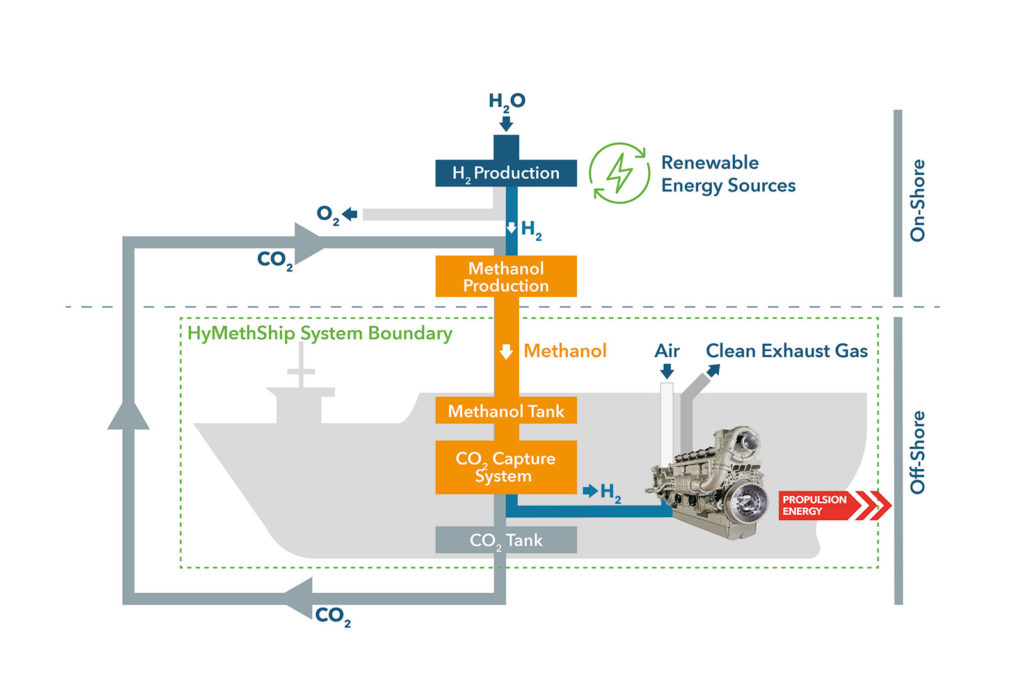
There is another advantage to bunking methanation fuels and reforming to hydrogen. By storing only methanol and CO2 onboard, HyMethShip would eliminate the challenge of storing hydrogen, which even when liquefied requires around twice the tank capacity of LNG. But while engine technology to burn methane or methanol is mature, the same cannot be said for hydrogen.
Hydrogen engines
While there has been widespread interest in hydrogen-fuelled fuel cells for marine applications, combustion engines capable of burning hydrogen are rare, particularly in the marine sector. Wärtsilä has tested mixing hydrogen fuel with LNG in both dual-fuel and ‘single-fuel’, spark-ignited engines. It confirmed that its current dual-fuel engines can use a fuel blend comprising around 25% hydrogen. Higher proportions are likely to require modifications.
Mono-fuel hydrogen engines and those that can run on hydrogen and diesel are emerging. One shipowner leading the way is CMB. Last month the Belgian company acquired Revolve Technologies, which built the engines for CMB’s passenger boat Hydroville, the world’s first sea-going vessel with dual-fuel diesel-hydrogen engines.
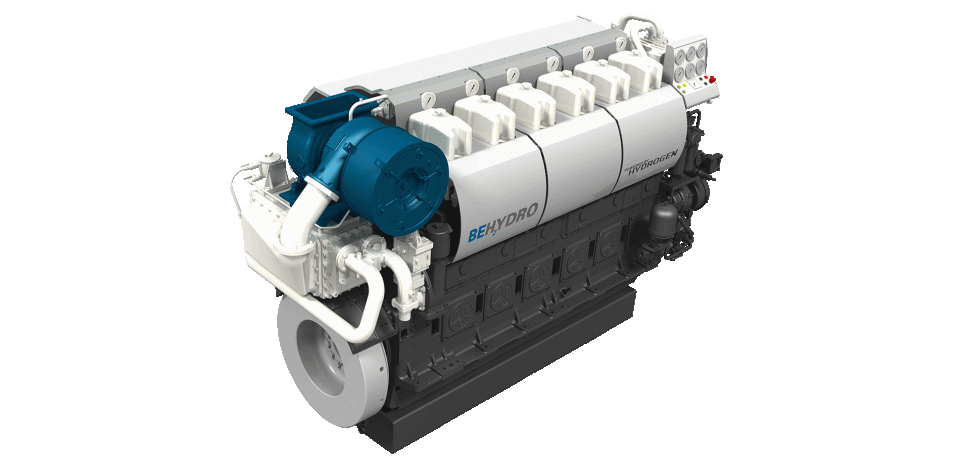
In a separate but related move, CMB announced last week that its BeHydro joint venture with engine builder Anglo Belgian Corporation will launch medium-speed hydrogen and hydrogen-diesel engines next year. They will be the first medium-speed marine engines to run on hydrogen, enabling bigger vessels to consider the fuel. Initially with six to 16 cylinders and a power output of up to 2.8 MW, the engines could be deployed as main engines on tugs, ferries and barges or as auxiliary engines on sea-going ships.
At this early stage there are plenty of options for the progressive shipowners and shipyards exploring the potential of methanation, including whether to opt for methane, methanol or hydrogen engine technologies. One way or another, these fuels will play a key role in the decarbonisation of shipping.