Press release (Vale): As of next days, the fleet of ships serving Vale will include the first large ore carrier in the world equipped with rotor sails. The VLOC (Very Large Ore Carrier) is a Guaibamax, with 325,000 tons of capacity. There are five sails installed along the vessel that will allow a gain in efficiency of up to 8% and a consequent reduction of up to 3,400 tons of CO2 equivalent per ship per year. If the pilot proves efficient, it is estimated that at least 40% of the fleet will be able to use the technology, which would result in a reduction of almost 1.5% of Vale’s annual iron ore maritime transport emissions.
Rotor sails are cylindrical rotors, four meters in diameter and 24 meters high – equivalent to a seven-story building. During operation, the rotors rotate at different speeds, depending on the environmental and operational conditions of the ship, to create a pressure difference in order to move the ship forward, due to a phenomenon known as the Magnus effect.
With Vale as project leader, the installation of the technology, provided by Finnish manufacturer Norsepower, had the partnership of Korean shipowner Pan Ocean to apply it in one of its VLOCs at Vale’s service. The Chinese design company Shanghai Ship and Design Research Institute (SDARI) was responsible for vessel design and integration with sail. The Chinese shipyard New Times Shipbuilding built the ship already adapted to receive the sails, which were installed at another shipyard, PaxOcean Engineering Zhoushan, also located in China. The Guaibamax is leaving China in the next days for Brazil, where it will receive the first shipment of iron ore at one of Vale’s ports in the country. On average, the trip takes 40 days.
“Our naval engineering team has been studying the use of wind propulsion technology for our business since 2016. With the Ecoshipping program we have developed several cooperation partnerships with ITV (Vale Institute of Technology), universities and laboratories in Brazil and Europe. For this project, the purpose was to evaluate the best operating conditions of rotor sails in our contracted fleet, and also validate the gains of this technology in terms of reducing fuel consumption and CO2 emissions,” explains Vale’s s shipping technical manager, Rodrigo Bermelho.
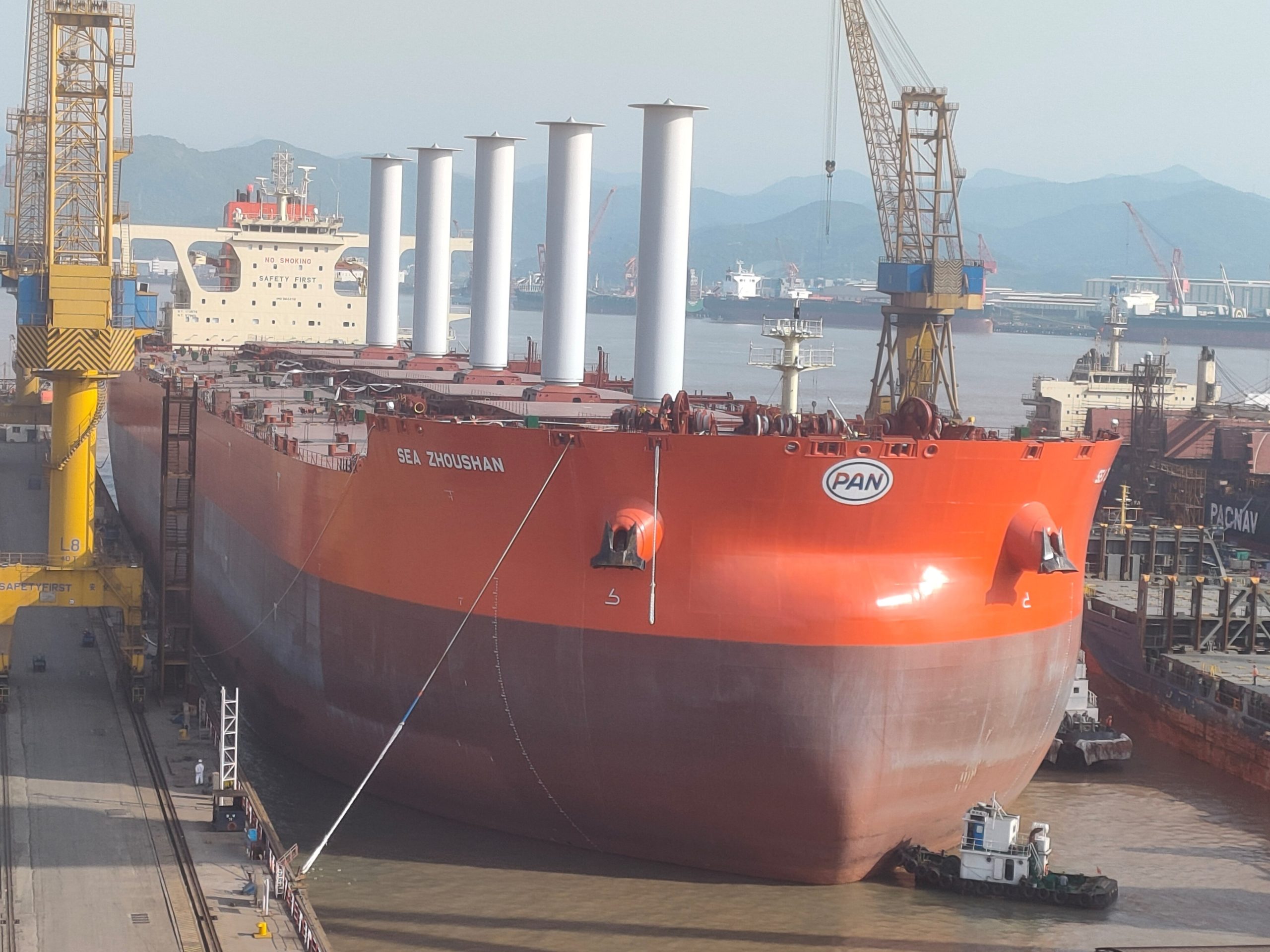
There are five sails installed along the vessel that will allow a gain in efficiency of up to 8% and a consequent reduction of up to 3,400 tons of CO2 equivalent per ship per year
The ship chosen was already contracted to be built and the time between detailed design to manufacture and installation of the equipment was one year. In addition to laboratory tests and numerical analyses, the technicians studied the incidence of winds on the Brazil-China route. “We realized that we have a competitive advantage over our competitors: the Brazil-Asia route has more wind on average than that of Australia-Asia,” Bermelho adds. According to Vale’s manager, 3D models of all the company’s ports were made to analyze how the ship would be moored. The sails recline to allow the operation of the ship loader. “There is no interference during loading,” he says.
The technology has existed since the nineteenth century, but has been resumed more efficiently since the 1980s and only in recent years has it started to be used in large ships, such as passenger ships, cargo ships and oil tankers.
Carbon Footprint
The operation of the first ore carrier equipped with rotor sails is part of Ecoshipping, a program created by Vale’s shipping area to meet the company’s challenge of reducing its carbon emissions, in line with what is discussed within the International Maritime Organization (IMO). Last year, the company announced an investment of at least USD 2 billion to reduce its scope 1 and 2 emissions by 33% by 2030. It also announced that it will reduce scope 3 emissions by 15% by 2035, related to the value chain, of which shipping emissions are part, given that the ships are not owned. These goals are aligned with the ambition of the Paris Agreement.
At the beginning of June, Vale is expected to receive the first Guaibamax ship with Air Lubrication installed. The technology creates a carpet of air bubbles at the bottom of the ship, allowing a reduction in water friction with the hull. Conservative expectations point to a fuel reduction of around 5 to 8%, with the potential to reduce annual emissions in Vale’s iron ore shipping by 4.4%.
In addition, Vale has been preparing for the adoption of alternative fuels. Dozens of second-generation VLOCs already in operation have been designed for future liquefied natural gas (LNG) system installation, including an under-deck compartment to receive a tank with capacity for the entire voyage. The Ecoshipping program is developing a multi-fuel tank capable of storing and consuming, in the future, not only liquefied natural gas (LNG), but also methanol and ammonia.
According to Bermelho, the adoption of energy efficiency technologies such as rotor sails and air lubrication will reduce the demand for fuel per ship and facilitate the adoption of low carbon fuels. A preliminary study for Guaibamax ships estimates that emission reductions can range from 40% to 80% when powered by methanol and ammonia, or up to 23% in the case of LNG.
Efficiency
With the adoption of new technologies and renewal of its fleet, Vale has invested heavily to incorporate the state of the art in terms of efficiency and environmental innovation in the shipping area. Since 2018, the company has operated with second generation Valemax ships and, since 2019, with Guaibamax ships, with capacities of 400,000 tons and 325,000 tons, respectively. These vessels are among the most efficient in the world and can reduce CO2 equivalent emissions by up to 41% compared to those of a 180,000-ton Capesize ship built in 2011.