Taking its lead from the healthcare sector, Biomicrogel has developed a new means of dealing with oil spills that works using nano-scale particles derived from agricultural waste products. Brian Dixon takes a look at the company for the latest in our ongoing profiles of startups.
Oil spills of one magnitude or another are an arguably all-too-regular occurrence for the maritime sector. However, Biomicrogel is a UK-registered startup that has developed a highly innovative new technology that could greatly improve the way the sector deals with these environmental hazards. “The history of our company started in 2012 when a group of young researchers were working on a problem of separating oil from water. Faced with the constraints of the conventional approaches, we decided to turn for inspiration to other industries and sectors. Our attention was drawn by biomicrogels that were used in healthcare,” says business development director Vladislav Perunov.
“Biomicrogels are nano-scale particles that on default are dissolved in water. However, if there is a change in the physical-chemical parameters of the water, such as salinity, hardness or pressure, biomicrogels start to form flocs. And if there is a contaminant that forms a phase boundary with water, then this floc formation happens at this very phase boundary,” he continues.
In healthcare, biomicrogels are used to encapsulate drugs in order to bypass certain organs while delivering the drug to the target location, where they then dissolve, releasing the drug. “Our discovery was that the very same property can be applied to water/oil mixtures and emulsions. Biomicrogels break down oil into small droplets, cover them with thin but firm films and bind them together. This ‘jellified’ oil has modified physical properties – it’s much easier to skim or remove from water,” he says, explaining that not only crude oil, but “any oily substance, such as mineral and vegetable oils, oil products, lubricants, fats and greases can be temporarily encapsulated”.
Meanwhile, “another breakthrough achievement was the development of a scalable production method for biomicrogels” as previously they could only be produced in small quantities and were therefore “quite expensive”. However, the company’s research has allowed it “to reduce the cost of biomicrogels, opening up the market for maritime applications”.
Indeed, the company produces two primary products for the maritime industry, with the first being a biomicrogel-based oil encapsulator (liquid sorbent) for the environmentally-friendly removal of oil spills from either water or land. “The encapsulator is supplied in dry form as a powder,” Perunov says, noting that as well as being “very compact” it is also “easy to transport and handle” and “can be stored for prolonged periods of time”. Before application, he continues, it is mixed with water to create a liquid that “can be applied on an oil spill with conventional sprayers from aboard a vessel” in the same manner as a traditional dispersant.
“The most praised quality that the biomicrogel-based encapsulator has is that it changes the viscosity of the oil and the oil slick doesn’t spread. This is a property that the oil spill response industry has been in search of for decades,” he says. Moreover, in addition to being easy to skim from the surface of the water, the jellified oil “doesn’t catch fire easily and it doesn’t stick to objects”, including wildlife, while protecting “the coastline and plants from oil pollution”.
But that’s not all. The “unique feature of the encapsulator”, he says, is that the oil/water/biomicrogel mixture can then be separated, meaning “the oil can be recovered and used for its original purpose”. Additionally, the used biomicrogels can be disposed of in a safe and environmentally-friendly manner “via bacteria treatment or used as fuel after drying”.
Furthermore, the company also produces a cloth impregnated with biomicrogels that can be used as a semi-permeable filtering material. “This material is capable of retaining a 200-mm high column of oil products while [allowing] water through. This quality makes the cloth suitable for the production of various membranes, filters or skimmer heads,” Perunov reports.
“The potential of biomicrogel-based products for the maritime industry is exceptional,” he states. “Biomicrogels can deliver solutions that can transform the core approaches in the oil spill clean-up sector, enhancing environmental and health and safety agendas.”
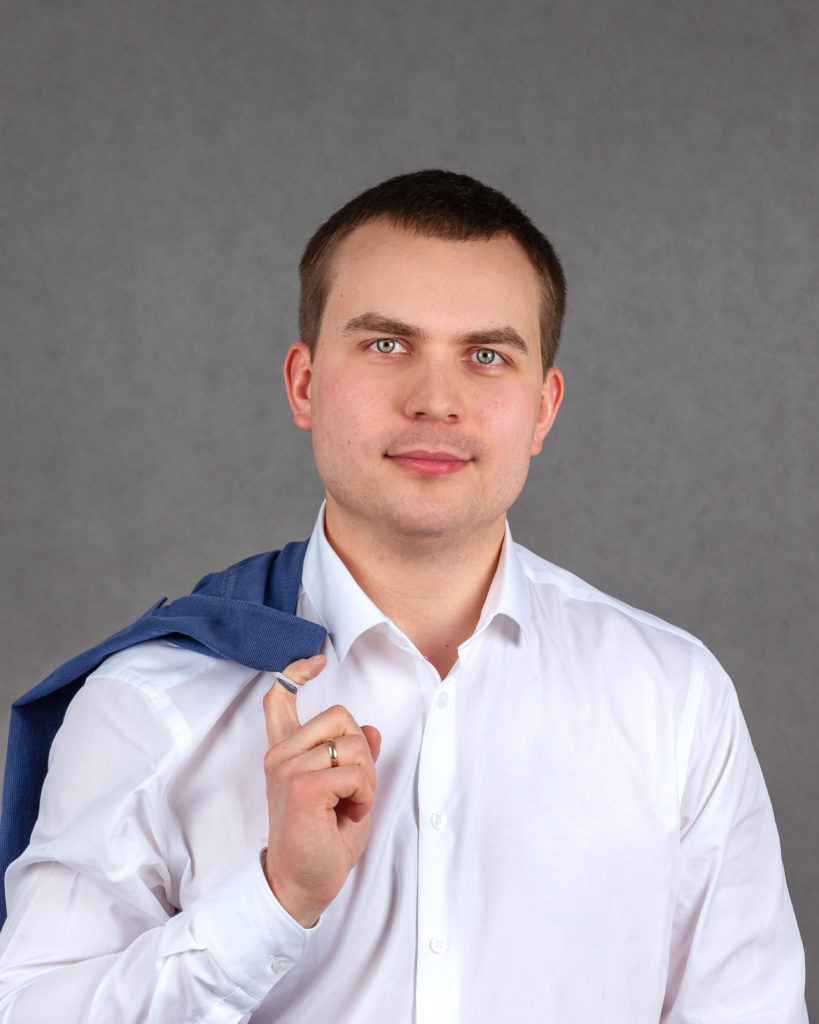
“The uniqueness of biomicrogels is determined by its feedstock,” he continues. “Biomicrogels have ‘bio’ in their name because they are produced from natural ingredients – agricultural wastes, such as apple or sugar beet pomace [or] cellulose. These wastes are essentially polysaccharides (for example, pectins) and biomicrogels are a special form of polysaccharides. As such, biomicrogels have unparalleled environmental credentials – they are completely biodegradable and safe for the environment.”
So far, the company has tested its biomicrogel-based encapsulator “in a simulated environment – a large enclosed pool where an oil spill was simulated – with big success”. Indeed, with its products having been tested as “absolutely safe and biodegradable”, it is now “hoping to have a chance to test [its] solution in a real-world setting within the Port XL accelerator” in which the company is currently participating.
More information on Biomicrogel, which, among other things, last year received a Seal of Excellence from the European Commission for its Horizon 2020 SME Instrument grant submission while also reaching the semi-finals of the FAMAE Precious Water Challenge Top 100, can be found at the company website