Press Release: New testing centre for large electric drive systems begins operations and provides industry with big opportunities.
Finland-based Yaskawa Environmental Energy / The Switch is powering forward with its vision to create bigger and ever more efficient electric drive systems with the start of operations at its heavyweight Large Drive Testing Centre (LDTC) in Lappeenranta in the south-east of the country.
This state-of-the-art testing centre can provide some of the answers to questions being asked by the maritime sector as shipowners, system integrators and shipyards navigate towards a greener future, while also looking to cut costs through better performance, greater efficiencies and improved reliability.
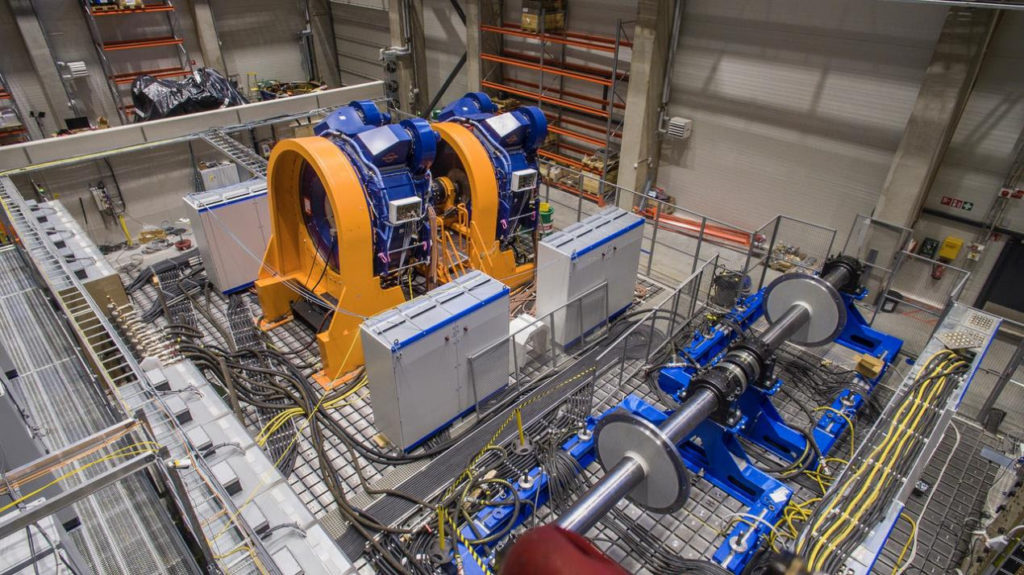
Credits Yaskawa Environmental Energy/The Switch
Yaskawa Environmental Energy / The Switch produces its permanent magnet (PM) direct-drive shaft generators, propulsion machines and auxiliary generators at Lappeenranta and it has built a track record of providing industry with energy efficient systems capable of delivering savings throughout the lifetime of a vessel.
The trend across the marine sector has been to move to increasingly higher capacity propulsion systems to power larger and larger vessels and the new testing centre can now push the boundaries for the biggest machines in the business.
Giant capacity
The centre can handle 12-megawatt drive systems, and this will increase soon to a giant 18 MW, outstripping almost anything else being offered across the globe. It also has a whopping 80-tonnes heavy-lift capacity.
Matti Nikkinen, vice president of operations at Yaskawa Environmental Energy / The Switch, says: ”Equipment is getting bigger and bigger all the time. We had to have a place where we can verify these units. It is important we can show the customer that our equipment can pass all the tests.
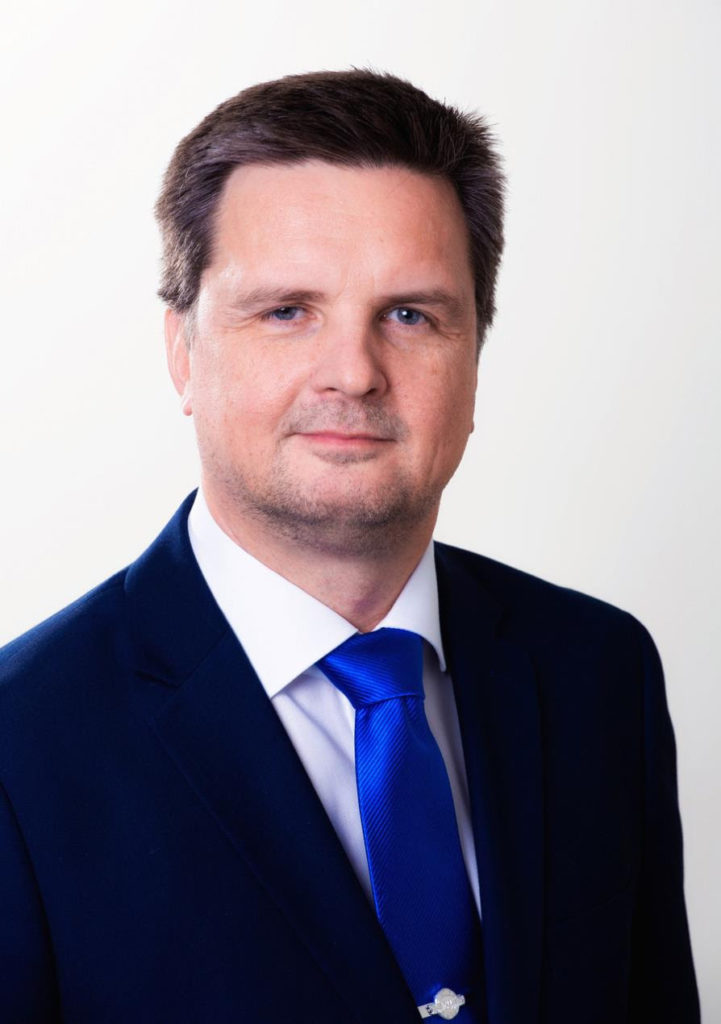
Credits Yaskawa Environmental Energy / The Switch
”Drives are continuously getting more powerful. So the main purpose for the testing facility is we can now answer the questions coming from the market.”
The new centre is attached to the main factory at Lappeenranta so finished units can be extensively tested to full capacity and complete certification can be carried out on site. This saves time and money down the line when it comes to the commissioning phase for any vessel using the equipment.
The test centre is nimble for such a heavy hitter as it offers a great deal of flexibility.
It can combine overall machine testing with the customer’s own components, such as their own shaft, bearings, beds or drives, or provide space for whole units brought in by customers.
Key objective
Tying the LDTC to the production factory also fulfils a key objective for Yaskawa Environmental Energy / The Switch as it means the centre is ideally placed for testing prototypes, enabling greater research, development and innovation.
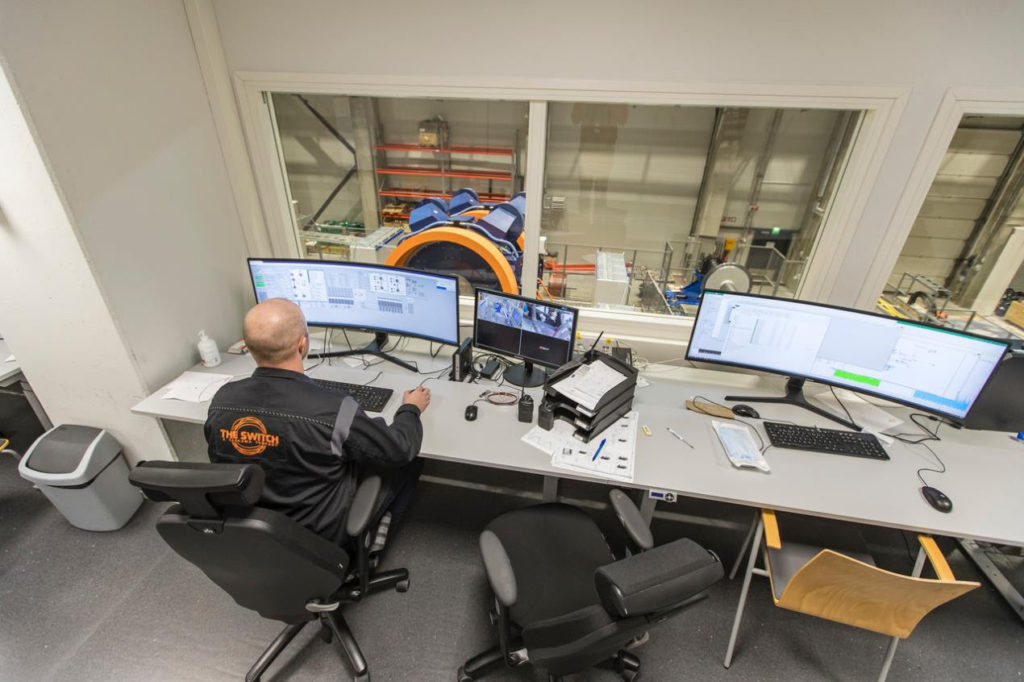
Credits Yaskawa Environmental Energy/The Switch
”The testing area is in the same factory as we have the production, so it is very easy to accommodate in that sense. The logistics are rather easy,” adds Mr Nikkinen.
”We can test any electric machine and drive. Currently, we have wind and marine products being tested.
”Normally there are two units at the same time in the testing area. One of these machines is run as a motor and the other as a generator,” says Mr Nikkinen. ”We will load identical machines, so we can test to full power and also measure all the required parameters to fully verify the systems.”
The centre has the space to run one full test while another is being prepared, which shortens the throughput time of the units.
Mr Nikkinen estimates the centre can process about 50 tests per year, depending on the size of the machines, which commonly comprise at least several megawatts and weigh in at 20 to 30 tonnes.
Marine generators will take roughly 65% to 70% of the time capacity over the course of the centre’s first full year in operation.
These marine generators have applications across a range of ship types, including bulk carriers, LNG vessels, subsea construction and offshore supply vessels, as well as being suitable for wind turbines.
The PM generators can be retrofitted and they come into their own with newbuilds, especially as emissions regulations tighten and shipowners have to find solutions with new technologies.
Big savings
Stricter legislation means modern ships will be required to reduce their total fuel consumption by up to 40%. Electric direct-drive systems like PM generators can play a central role in achieving that, future-proofing vessels and saving ship operators significant sums over the lifespan of a vessel.
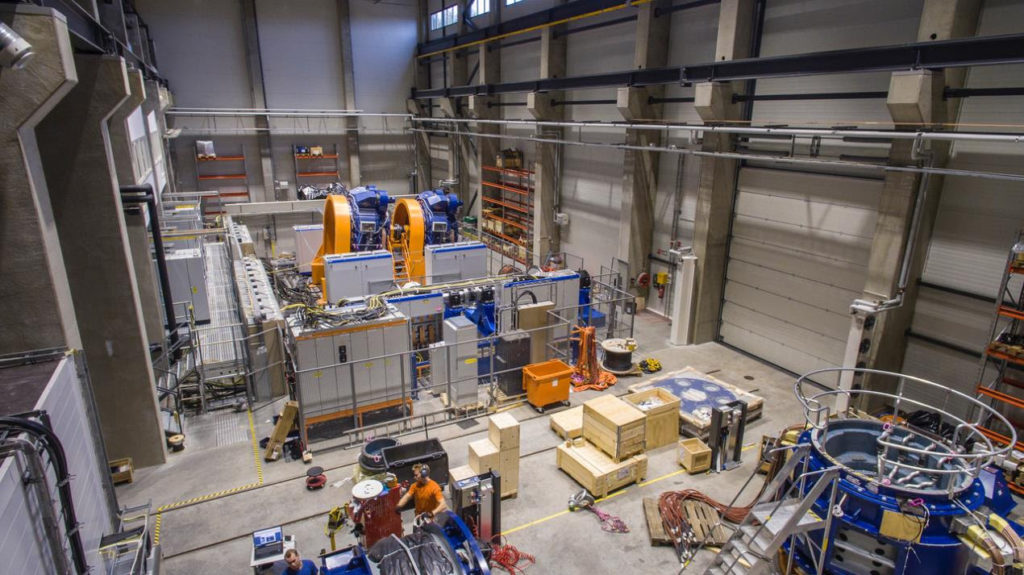
Credits Yaskawa Environmental Energy/The Switch
”The energy efficiency is very high in PM generators. They have fewer components, so especially the rotor side of the machine is very simple compared with earlier technologies,” says Mr Nikkinen.
”The reliability is high as a result. The machines are simple and the maintenance costs are very competitive.”
The prospect of built-in cost savings over the lifetime of a vessel in the marine sector should draw any shipowner to the table like a magnet.
Yaskawa Environmental Energy / The Switch’s new testing centre offers the chance to extensively test systems and provide full verification, giving ship owners peace of mind. Surely an attractive proposition.
”This kind of testing centre does not exist in many places around the world… and we are now in a position to fulfil our own requirements while helping customers attain more effective and more efficient products for the future,” adds Mr Nikkinen.